Porosity in Welding: Identifying Common Issues and Implementing Finest Practices for Prevention
Porosity in welding is a prevalent problem that typically goes unnoticed until it creates substantial troubles with the integrity of welds. In this discussion, we will explore the key elements contributing to porosity formation, analyze its damaging impacts on weld performance, and talk about the finest methods that can be embraced to minimize porosity occurrence in welding processes.
Typical Reasons For Porosity
An additional regular wrongdoer behind porosity is the existence of contaminants on the surface area of the base metal, such as oil, oil, or corrosion. When these contaminants are not properly removed prior to welding, they can evaporate and become caught in the weld, causing flaws. Using filthy or damp filler materials can present impurities right into the weld, contributing to porosity concerns. To alleviate these common root causes of porosity, detailed cleaning of base metals, appropriate securing gas selection, and adherence to optimal welding specifications are crucial practices in achieving top notch, porosity-free welds.
Impact of Porosity on Weld High Quality

The existence of porosity in welding can substantially jeopardize the architectural stability and mechanical buildings of bonded joints. Porosity develops voids within the weld steel, weakening its total toughness and load-bearing ability. These voids serve as tension concentration points, making the weld a lot more prone to fracturing and failing under used lots. Additionally, porosity can reduce the weld's resistance to corrosion and other ecological factors, further diminishing its longevity and performance.
Welds with high porosity levels often tend to exhibit lower influence stamina and lowered ability to warp plastically prior to fracturing. Porosity can hinder the weld's capacity to effectively transfer forces, leading to early weld failure and potential security threats in vital frameworks.
Best Practices for Porosity Prevention
To improve the structural integrity and quality of welded joints, what particular measures can be implemented to decrease the event of porosity throughout the welding process? Using the proper welding method for the certain material being welded, such as readjusting the welding angle and weapon setting, can check my reference even more prevent porosity. Normal assessment of welds and immediate removal of any type of problems identified throughout the welding process are essential methods to stop porosity and produce top quality welds.
Importance of Correct Welding Methods
Executing correct welding strategies is critical in guaranteeing the structural integrity and quality of bonded joints, building on the foundation of efficient porosity prevention actions. Welding methods straight affect the total stamina and resilience of the bonded structure. One crucial aspect of appropriate welding techniques is preserving the correct warmth input. Extreme warm can lead to boosted porosity due to the entrapment of gases in the weld swimming pool. Conversely, inadequate warmth may lead to insufficient combination, developing potential weak factors in the joint. In addition, using the proper welding parameters, such as voltage, present, and take a trip rate, is important for attaining sound welds with very little porosity.
Additionally, the option of welding procedure, whether it be MIG, TIG, or stick welding, need to straighten with the specific requirements of the project to guarantee ideal outcomes. Appropriate cleaning and prep work of the base metal, as well as choosing the right filler material, are likewise essential components of skillful welding techniques. By sticking to these finest techniques, welders can lessen the risk of porosity formation and create top quality, structurally audio welds.
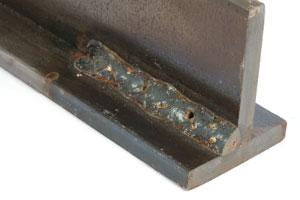
Testing and Quality Assurance Steps
Quality control measures play an important function in validating the integrity and integrity of welded joints. Testing procedures are necessary to identify and avoid porosity in welding, guaranteeing the toughness and sturdiness of the last item. Non-destructive screening methods such as ultrasonic screening, radiographic screening, and published here aesthetic examination are typically used to recognize potential flaws like porosity. These strategies enable the assessment of weld high quality without compromising the honesty of the joint. What is Porosity.
Performing pre-weld and post-weld inspections is also essential in maintaining quality assurance criteria. Pre-weld inspections include confirming the products, equipment setups, and cleanliness of the workspace to avoid contamination. Post-weld inspections, on the various other hand, assess the final weld for any type of defects, including porosity, and verify that it fulfills defined criteria. Implementing a detailed quality assurance plan that consists of these details thorough testing procedures and inspections is extremely important to reducing porosity issues and guaranteeing the general quality of welded joints.
Final Thought
To conclude, porosity in welding can be an usual concern that impacts the top quality of welds. By recognizing the typical reasons for porosity and executing ideal techniques for prevention, such as correct welding strategies and screening measures, welders can make sure premium quality and reliable welds. It is necessary to focus on avoidance approaches to reduce the incident of porosity and keep the integrity of bonded structures.